There are several common complaints with Punto mk2 front window wiper mechanism:
1. Judder, often caused by non-conducting electrical grease having been inappropriately used. Fix with the right grease
2. Link arms dropping off, caused by unavoidable wear in the connecting ball-and-socket link arm. Fix with new arm, or a repair clip, or a retaining device (welded washer, split pin, self tapper, ...)
3. The wiper arm experiencing wander. This can show up as the rest position varying when the wipers are on (one minute, striking the scuttle with a whack, next minute, normal operation).
This guide is a DIY solution for #3 above. The other 2 have been covered well elsewhere.
Note that it is not possible to buy any of the wiper mechanism components separately as an OEM part, you have to shell out for the whole assembly. The cost for this assembly is currently ~£60. You might get one at a scrapyard (mk2 mechanisms disappear quickly!), but they could be worn too, so check carefully. They currently go for ~£25 and up. Non OEM replacement links are available.
Safety
Make sure the key is removed from the ignition. You don't want the wiper arms to move when you are working on them, the motor is strong and you don't want to lose a finger.
Problem
The problem I had on my front passenger side is the blade striking the scuttle for a while, then operating normally, then back to striking the scuttle, in a fairly random way. Apart from being really annoying, it results in additional wear to the mechanism, the blades wearing out more quickly, and the scuttle being marked.
Diagnosis
Grab the wiper arm at its base near the retaining nut, and move back and forth. If there is appreciable motion, you probably have a worn bush. Adjusting the position of the wiper arm on the spindle will not fix this.
First, orientation:
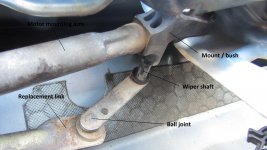
The wiper mechanism is attached to the car through 2 plastic mounts. These serve 2 functions:
1. As a mount - you can see the fixed motor arm that goes from this plastic mount to the motor. There is another one on the other side.
2. As a bush for the wiper shaft. In this image, I have dropped the shaft for clarity.
You can also see the infamous ball joint, which connects to the wiper shaft with a short link. I replaced these a while ago with replacement links from Wipex, which are at end of life now after a few years.
The wiper shaft rotates in the bush, classic rotary bearing. Unfortunately, the bush is made from Nylon (you can see the PA, for polyamide, stamp on the plastic moulding). This means it wears out.
Once the wiper arm is off (13mm spanner and a bit of pulling), you will see this:
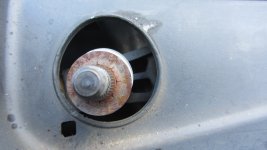
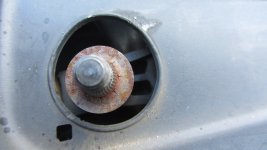
This shows that the shaft is moving in the bush. There should be no lateral motion.
The shaft is retained in the bush with a starlock washer, which sits on top of a plain washer, which sits on top of the face of the bush. The shaft has an OD of 10mm, the plain washer has a matching ID of (approx.) 10mm.
The starlock washer can be carefully pried off with a flat screwdriver, and the plain washer can be recovered.
You'll then see wear like this in the bush:
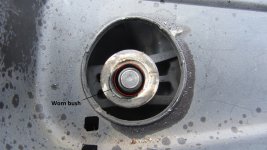
What should be a circular bush has worn into an elongated oval. This allows the wiper shaft to wander, and the position of the wiper arm to vary as a result.
The solution is to return the top of the bush to the marked circular shape. I cleaned the plain washer (18mm OD, 10mm ID) and the top of the bush with 180 grit sandpaper, see below.
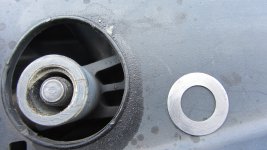
I then used 2 part epoxy glue (generic, although next time I might go for Q Bond, which looks very strong in the demos I've seen) to glue the plain washer to the bush. It's easy to get this right - the washer outer diameter matches the bush so you can get it nicely centralised.
Refit the starlock. You can replace with a 10mm starlock if preferred, mine was OK to reuse. Reconnect the wiper arm. Test.
Mine seems to be fixed now, no more striking the scuttle.
There are two additional options I can see if this does not turn out to be reliable:
1. Drill out the bush with a 12mm drill. Glue in a length of 12mm OD, 10mm ID stainless seamless pipe, hand cut to length. This should prove reliable, as the glue surface area is much larger.
2. Get a 12mm OD, 10mm ID (custom probably) made that fits inside a small recess in the top of the bush. Then glue the plain washer on top of this.
I will monitor my current solution and see how reliable it is over the next while
1. Judder, often caused by non-conducting electrical grease having been inappropriately used. Fix with the right grease
2. Link arms dropping off, caused by unavoidable wear in the connecting ball-and-socket link arm. Fix with new arm, or a repair clip, or a retaining device (welded washer, split pin, self tapper, ...)
3. The wiper arm experiencing wander. This can show up as the rest position varying when the wipers are on (one minute, striking the scuttle with a whack, next minute, normal operation).
This guide is a DIY solution for #3 above. The other 2 have been covered well elsewhere.
Note that it is not possible to buy any of the wiper mechanism components separately as an OEM part, you have to shell out for the whole assembly. The cost for this assembly is currently ~£60. You might get one at a scrapyard (mk2 mechanisms disappear quickly!), but they could be worn too, so check carefully. They currently go for ~£25 and up. Non OEM replacement links are available.
Safety
Make sure the key is removed from the ignition. You don't want the wiper arms to move when you are working on them, the motor is strong and you don't want to lose a finger.
Problem
The problem I had on my front passenger side is the blade striking the scuttle for a while, then operating normally, then back to striking the scuttle, in a fairly random way. Apart from being really annoying, it results in additional wear to the mechanism, the blades wearing out more quickly, and the scuttle being marked.
Diagnosis
Grab the wiper arm at its base near the retaining nut, and move back and forth. If there is appreciable motion, you probably have a worn bush. Adjusting the position of the wiper arm on the spindle will not fix this.
First, orientation:
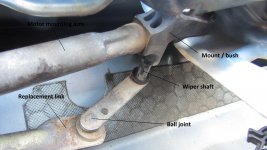
The wiper mechanism is attached to the car through 2 plastic mounts. These serve 2 functions:
1. As a mount - you can see the fixed motor arm that goes from this plastic mount to the motor. There is another one on the other side.
2. As a bush for the wiper shaft. In this image, I have dropped the shaft for clarity.
You can also see the infamous ball joint, which connects to the wiper shaft with a short link. I replaced these a while ago with replacement links from Wipex, which are at end of life now after a few years.
The wiper shaft rotates in the bush, classic rotary bearing. Unfortunately, the bush is made from Nylon (you can see the PA, for polyamide, stamp on the plastic moulding). This means it wears out.
Once the wiper arm is off (13mm spanner and a bit of pulling), you will see this:
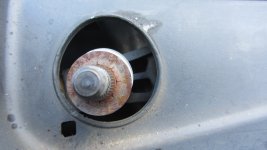
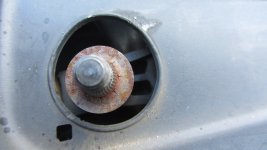
This shows that the shaft is moving in the bush. There should be no lateral motion.
The shaft is retained in the bush with a starlock washer, which sits on top of a plain washer, which sits on top of the face of the bush. The shaft has an OD of 10mm, the plain washer has a matching ID of (approx.) 10mm.
The starlock washer can be carefully pried off with a flat screwdriver, and the plain washer can be recovered.
You'll then see wear like this in the bush:
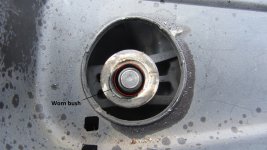
What should be a circular bush has worn into an elongated oval. This allows the wiper shaft to wander, and the position of the wiper arm to vary as a result.
The solution is to return the top of the bush to the marked circular shape. I cleaned the plain washer (18mm OD, 10mm ID) and the top of the bush with 180 grit sandpaper, see below.
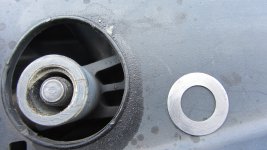
I then used 2 part epoxy glue (generic, although next time I might go for Q Bond, which looks very strong in the demos I've seen) to glue the plain washer to the bush. It's easy to get this right - the washer outer diameter matches the bush so you can get it nicely centralised.
Refit the starlock. You can replace with a 10mm starlock if preferred, mine was OK to reuse. Reconnect the wiper arm. Test.
Mine seems to be fixed now, no more striking the scuttle.
There are two additional options I can see if this does not turn out to be reliable:
1. Drill out the bush with a 12mm drill. Glue in a length of 12mm OD, 10mm ID stainless seamless pipe, hand cut to length. This should prove reliable, as the glue surface area is much larger.
2. Get a 12mm OD, 10mm ID (custom probably) made that fits inside a small recess in the top of the bush. Then glue the plain washer on top of this.
I will monitor my current solution and see how reliable it is over the next while